In the world of improving processes and making them more efficient, we often come across terms like lead time, takt time and cycle time.
These concepts are important in different industries, like manufacturing or services.
While they may seem similar, each one represents a different part of the overall process. Understanding what they are, and how they are different and similar can help you tremendously.
In this article, we will explore these aspects in depth.
What is takt time? Takt time definition
Takt time is the available time per unit to meet customer demand. It’s calculated by dividing the available time by the customer demand.
This metric is primarily used in manufacturing or production process environments to determine the production time needed to meet customer demand.
It sets the pace at which products need to be finished to ensure that customer requirements are fulfilled.
Example of takt time calculation:
Let's assume you have an 8-hour shift and the customer demand is 400 units per day.
To calculate the takt rate, you divide the available time by the customer demand.
Takt time formula:
Operable takt time = available time/customer demand
Operable takt time = 8 hours/400 units per day
Operable takt time = 0.02 hours per unit
Therefore, the takt rate for this scenario is 0.02 hours per unit.
Why calculate takt time?
The main reason is that it serves several benefits in process workforce optimization.
Benefit 1: Meeting customer demand
Calculating takt time allows organizations to align their production rate with customer demand. It helps to make sure that products are manufactured at the required pace to meet customer requirements effectively.
Benefit 2: Preventing overproduction or underproduction
It also helps in avoiding overproduction, which can lead to excess inventory and waste. Similarly, it prevents underproduction. This way, customer demand is adequately met without delays or shortages. In short: perfect production time is maintained.
Benefit 3: Optimizing resource allocation
Finally, tracking these performance metrics is also great for optimizing resource allocation. By understanding takt time, your company can manage resources efficiently. Thanks to this, you can plan workforce, equipment, and materials based on the needed production rate.
The result? You avoid unnecessary costs or shortages.
What is cycle time? Cycle time definition
Cycle time refers to the time it takes to complete one cycle of an entire production cycle.
It’s measured in seconds and calculated by dividing the operating time by the quantity produced. Cycle time can be used to analyze and improve individual process steps or operations within a larger workflow.
Example of cycle time formula
Machine setup time: 1 hour
- Processing time per unit: 0.5 hours
- Inspection time per unit: 0.25 hours
To calculate the cycle time, you add up all the times:
Cycle time = machine setup time + processing time per unit + inspection time per unit
Cycle time = 1 hour + 0.5 hours + 0.25 hours
Cycle time = 1.75 hours
Therefore, the cycle time for this process is 1.75 hours.
Why calculate cycle time?
Similarly to tracking takt time, measuring cycle time can do wonders as well.
Benefit 1: Identifying bottlenecks and inefficiencies
Pinpointing process bottlenecks, inefficiencies, or variations becomes a breeze when you track cycle time. That’s because it allows companies to identify areas that require improvement. The outcome? Streamlined workflows and reduced waste.
Benefit 2: Improving productivity and throughput
Another great advantage is the opportunity to boost productivity and increase throughput. Shorter cycle times enable faster completion of processes, leading to more efficient operations and higher output.
Benefit 3: Enabling process optimization
Analyzing cycle time provides insights into individual process steps or operations. This information helps in optimizing workflows, eliminating non-value-added activities, and improving overall efficiency.
What is lead time? Lead time definition
Lead time is the time it takes for a customer order to be fulfilled from the start to the finished product or service. It includes the pre-processing time required to prepare the product, as well as any waiting time in queues or transit and post-processing time. Lead time is often measured in days or weeks.
Example of lead time calculations:
- Processing time: 8 hours
- Waiting time: 4 hours
- Inspection time: 2 hours
To calculate the lead time, you simply add up all the times:
Lead time = Processing time + Waiting time + Inspection time
Lead time = 8 hours + 4 hours + 2 hours
Lead time = 14 hours
Therefore, the delivery lead time for this manufacturing process is 14 hours.
Why calculate lead time?
Finally, tracking your lead time doesn’t go without benefits either.
Benefit 1: Managing customer expectations
Lead time calculation is essential for managing customer expectations. When you can understand the time required from order placement to delivery, your business can provide realistic and accurate delivery estimates. As a result, you can enhance customer satisfaction.
Benefit 2: Enabling proactive supply chain management
Another benefit is associated with effective planning of the production process, inventory, and supply chain activities. Tracking lead time aids in coordinating with suppliers, managing stock levels, and accurately estimating the actual production time.
Benefit 3: Identifying process delays and bottlenecks
Finally, with lead time, you can easily identify potential delays or bottlenecks in the order fulfillment process. Lead time lets companies take proactive measures to streamline processes, reduce waiting times, and improve overall operational efficiency.
Let Unrubble calculate takt time, cycle time & lead time for you
Now that you know why it’s worth tracking these measures, how about finding out… how you can actually do it?
When it comes to that, Unrubble’s time tracking solution can provide a seamless and efficient way.
Here's exactly how we can help:
Takt Time Measurement:
- use our employee work time tracker to monitor your employees' clock-ins and clock-outs, as well as their active work hours, including lunch breaks, time offs and any other additional breaks
- take advantage of accurate tracking of active working hours so that you can count the total work time for a specific period; easily determine the takt time.
- benefit from our convenient mobile app that employees can easily clock in and out in; let the app automatically record the time, ensuring precise measurement of takt time.
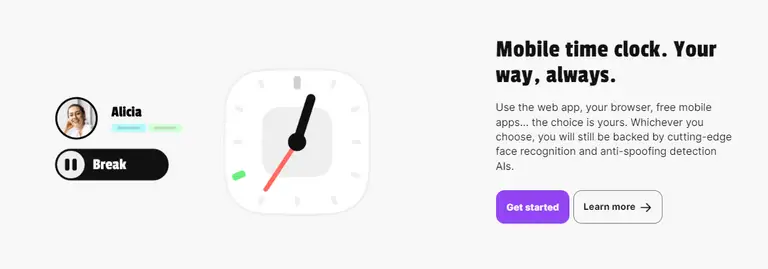
Cycle Time Measurement:
- our employee work time tracker provides you with a breakdown of workable hours for each employee, including start time and end time for specific tasks or processes
- thanks to analyzing the recorded work hours for different processes or tasks, you can calculate the cycle time for each step with Unrubble
- Unrubble's detailed work time tracking reports allow you to identify the time taken for individual tasks, helping you measure and optimize cycle times
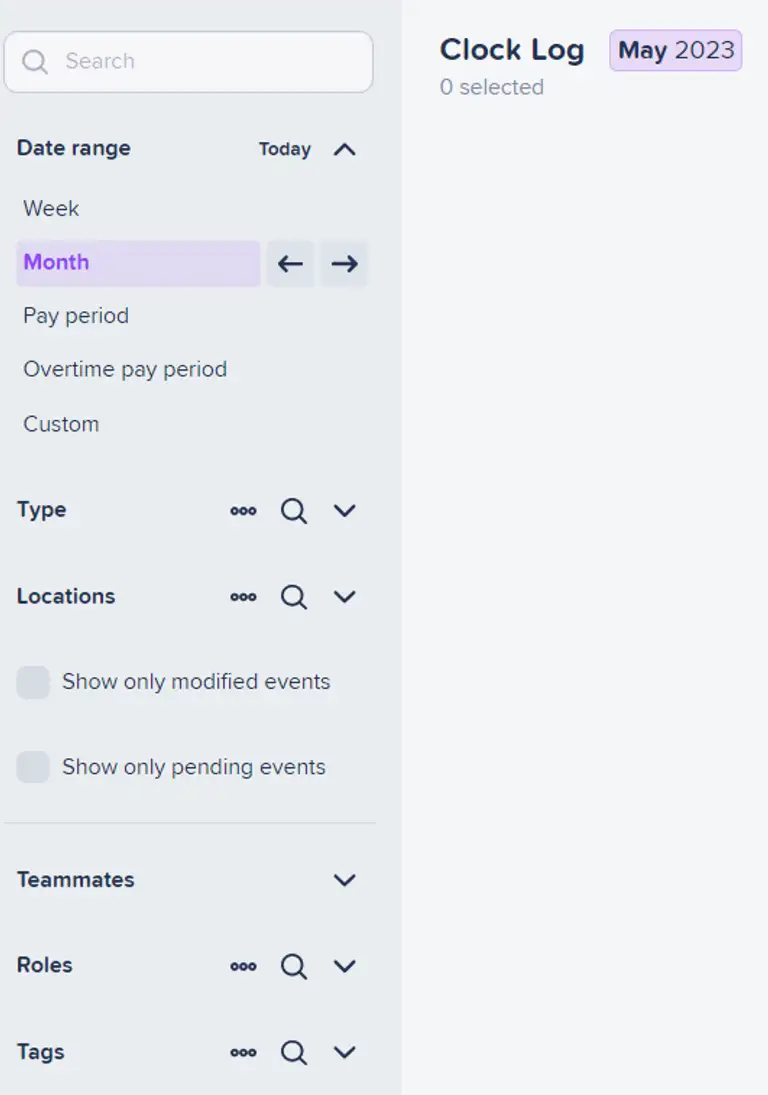
Lead Time Measurement:
- Unrubble's employee work time tracker lets you track the time between order placement and delivery by recording work hours and attendance for each employee involved in the order fulfillment process.
- you can easily record workable production hours and attendance data to calculate the lead time, which represents the overall time taken to fulfill an order
Our comprehensive reports provide insights into the time spent at each stage of the process, helping you identify potential delays and bottlenecks that affect lead time
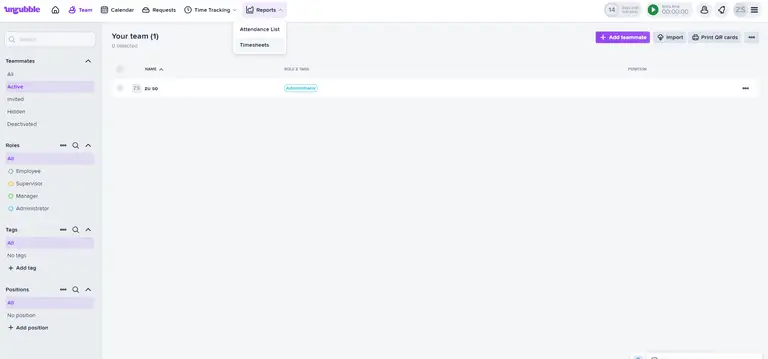
Why choose Unrubble for measuring these metrics?
Unrubble offers an all-in-one workforce management solution that includes time tracking, employee scheduling, leave management, and business travel management.
With a user-friendly interface and mobile app, Unrubble provides hassle-free and real-time tracking of work hours. In a nutshell, we ensure accurate measurements of takt time, cycle time, and lead time.
Our automation features eliminate manual data collection and calculation, saving time and reducing the chances of errors.
What’s more, our system generates detailed reports and timesheets ready for export to payroll apps.
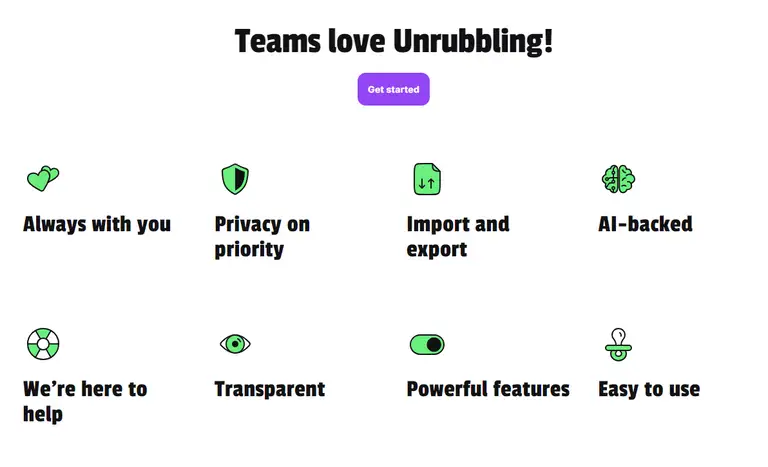
This way, it’s easy to analyze and utilize the metrics for process improvement and resource optimization.
We also provide expert support through chat, email, and phone to assist you in using the system effectively and maximizing the benefits of accurate metric measurement.
So don’t think too much about it and give Unrubble a try today. We guarantee you won’t regret it. Our 14-day trial period is waiting for you.
BONUS: takt vs cycle vs lead time comparison
Never confuse these 3 metrics again with our handy comparison sheet. Enjoy! Understand the differences between takt time, lead time, and cycle time. Here is how to calculate them.
Takt Time
- Definition: The actual time available per unit to meet demand.
- Purpose: Helps determine the production rate needed to meet customer demand.
- Calculation: Takt Time = Available Time / Customer Demand.
- Units: Usually measured in seconds per unit.
- Focus: Focuses on meeting customer demand by setting the production pace.
- Variation: Remains constant unless there are changes in customer demand.
- Improvement: Can be optimized by refining the production process or increasing available time.
- Importance: Assists in maintaining a balanced and efficient production flow.
Cycle Time
- Definition: The time it takes to complete one cycle of a process.
- Purpose: Helps identify the time required for each step in a process.
- Calculation: Cycle Time = Operating Time / Quantity Produced.
- Units: Usually measured in seconds.
- Focus: Concentrates on analyzing and improving individual process steps or operations.
- Variation: Can vary based on process improvements or changes in equipment or resources.
- Improvement: Can be reduced by eliminating waste, enhancing workflow, or increasing resources.
- Importance: Aids in identifying potential bottlenecks or inefficiencies.
Lead Time
- Definition: The time it takes for a customer order to be fulfilled from start to finish, including pre-processing and post-processing time.
- Purpose: Helps evaluate the overall time required to fulfill customer orders.
- Calculation: Lead Time = Processing Time + Waiting Time.
- Units: Usually measured in days or weeks.
- Focus: Focuses on evaluating the efficiency of the entire order fulfillment process.
- Variation: Influenced by factors such as process efficiency, supply chain delays, or order complexity.
- Improvement: Can be shortened by streamlining processes, reducing bottlenecks, or enhancing coordination.
- Importance: Ensures timely delivery and helps meet customer expectations regarding product quality and manufacturing operation.
Wrap Up
And that’s a wrap! You’ll never be confused again at the mention of lead, takt time and cycle time.
And if you like the idea of our Unrubble time tracking solution - don’t be shy and give it a try. Your best time tracking software is just a few clicks away. We promise we won’t disappoint you.